Why do you need a custom baseplate and where would you use a custom baseplate?
August 12th, 2020
Carver Pump manufactures a full line of vertical pumps. Our G2S (sump pump) and G2C (cantilevered vertical) models come with standard baseplates whose dimensions can be seen in our technical bulletin. Tech Book
How to Know When a Non-Standard Baseplate is Needed
What happens when your pump needs a non-standard baseplate? A custom baseplate might require a specialized shape, thickness, finish or tolerance. Below we outline some common examples. It’s probably easier than you think to make a custom baseplate. A laser-cutting or flame-cutting machine can produce the desired shape.
Using a DXF file or some other similar drawing format, specialized nesting software allows the laser cutter to efficiently fit many different jobs on one sheet, to minimize setup and material cost. This equipment makes the marginal cost of a customized baseplate very affordable compared to standard, off-the-shelf designs.
Perhaps the most common reason a facility would need a custom baseplate is to replace an existing pump. Over the years manufacturers have adopted different baseplate sizes and shapes. For example, Aurora’s models 530 and 531 used an oval shape. Below is a Carver Pump with an Aurora-style base.
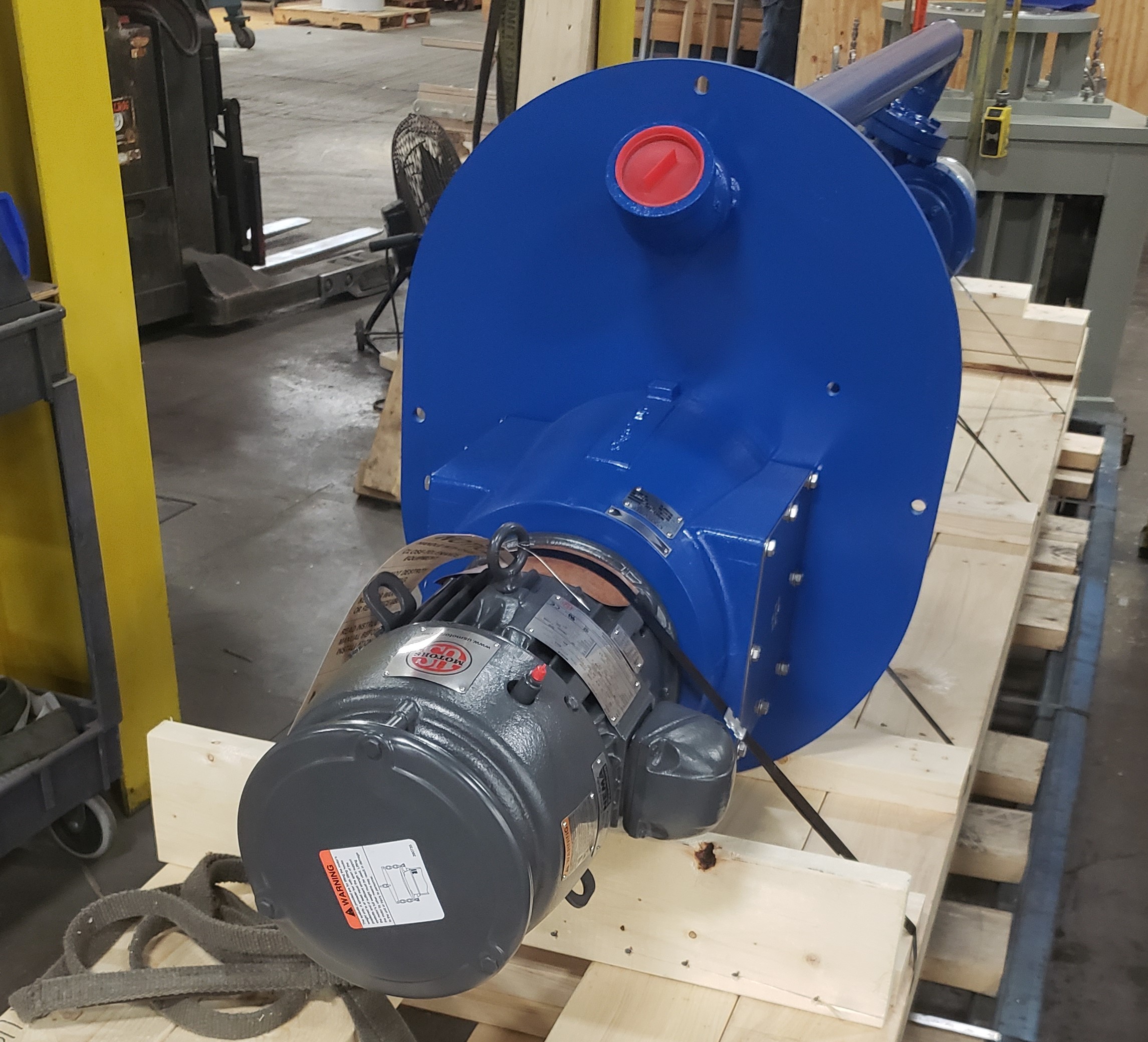
Carver Pump with Aurora Style Baseplate
Many other legacy companies, such as Chicago and Lawrence, had their own baseplate designs that sometimes needed to be duplicated.
A second custom baseplate scenario is that of the duplex sump pump. For decades, having two pumps on one baseplate was considered a way to reduce equipment and installation costs. More recently, this has fallen out of favor and many facility owners have elected to either install a single larger pump or two separate pumps on separate baseplates, to make removal and servicing of the pumps easier. Even so, the duplex installation is still seen in many industrial facilities, and the cost of building a single customized piece of equipment with two pumps on a single base plate may not be much different from buying two separate pumps.
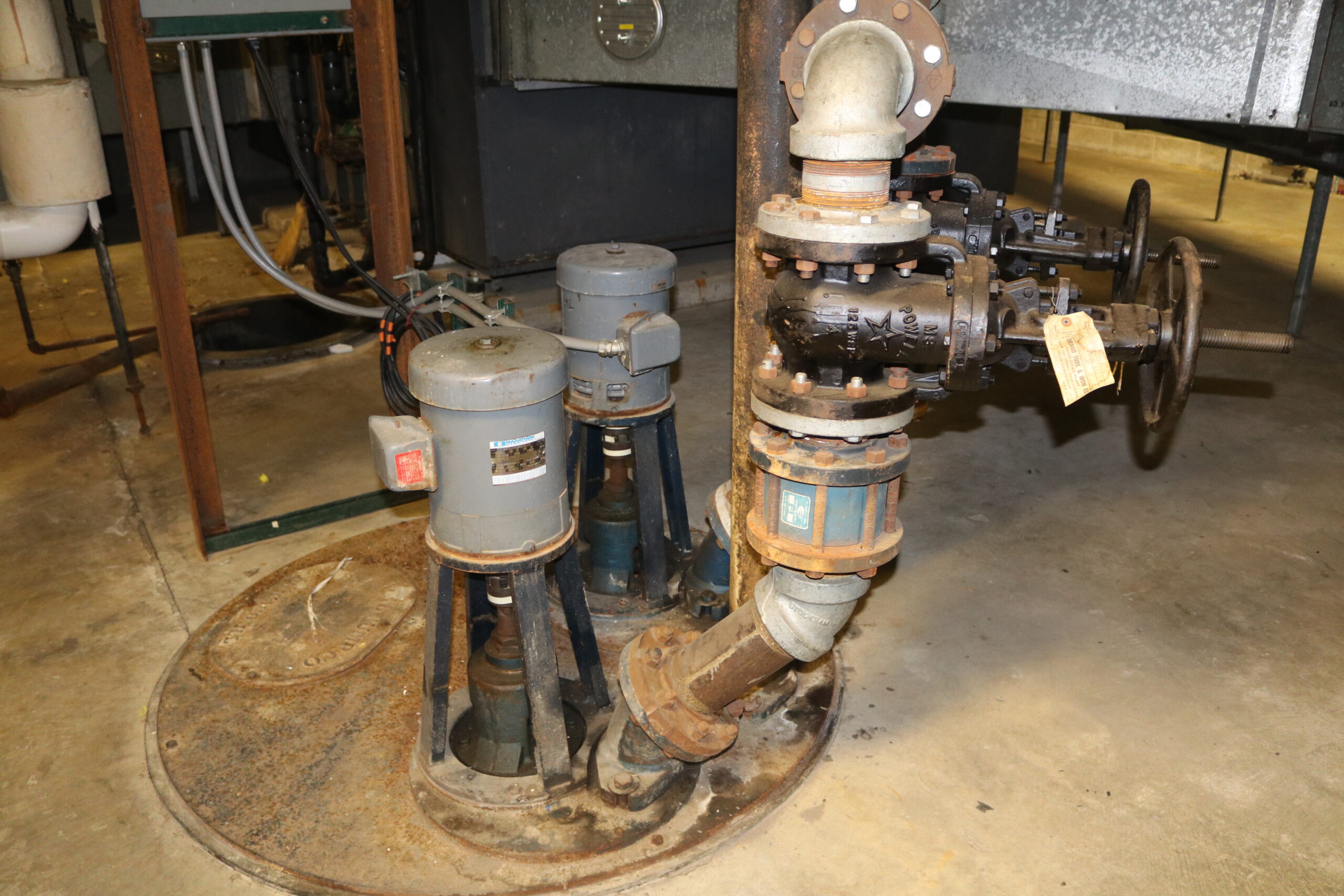
Baseplate with Two Pumps
Another case arises when a pump must be installed on top of a tank in vapor-tight locations. These baseplates are typically round with mounting holes around the perimeter so that the pump can be attached to the top of a tank. It can be machined to any dimensions on the underside, then gasket to achieve a vapor-tight installation.
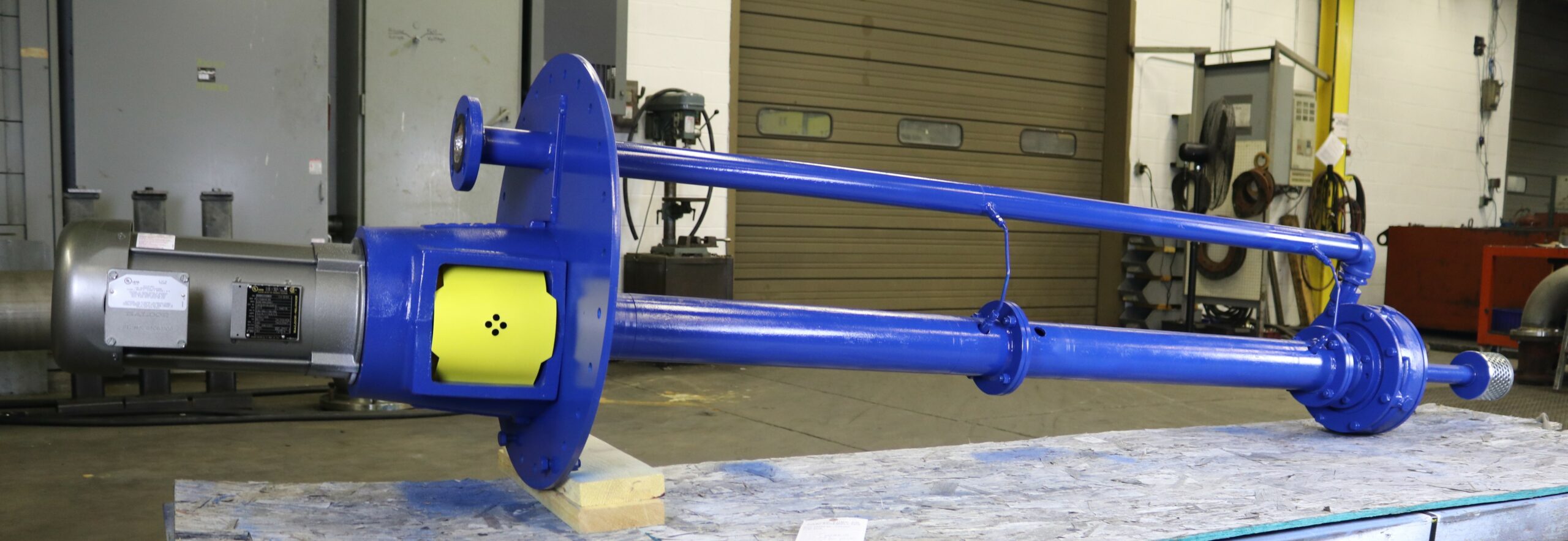
G2S with Round Base
Laser Cut or Flame Cut?
Laser cutting is the preferred method of making the baseplate shape when precise tolerance is required. A laser cutter can typically achieve tolerance for cuts of +/- 10 thousandths. For 1/2″ plates, this process can typically achieve flatness of 30 thousandths per foot.
Flame cutting is also a low-cost option for thicker plates but may result in a larger heat-affected zone and warp or coil reset. To achieve a high degree of flatness on thicker baseplates, it may be necessary to flame cut the plate to the desired shape and mill or Blanchard grind the surface to achieve the required flatness.
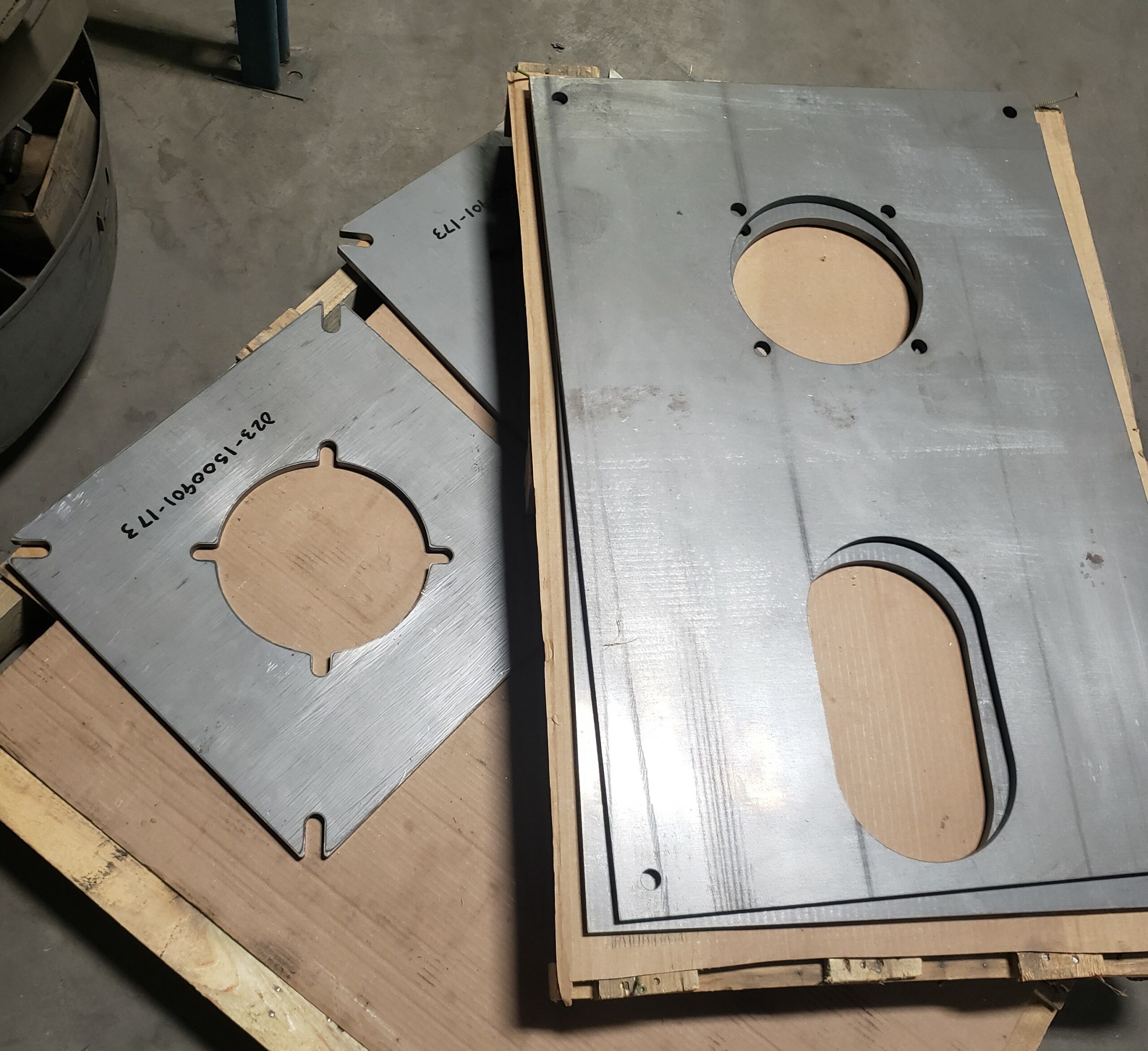
Laser Cut Baseplates
Conclusion
There are countless varieties of pump configurations available. With some advanced planning, you can select a design that achieves process requirements while minimizing project and maintenance costs.